科普:如何利用工业4.0制造一辆宝马新5系Li?
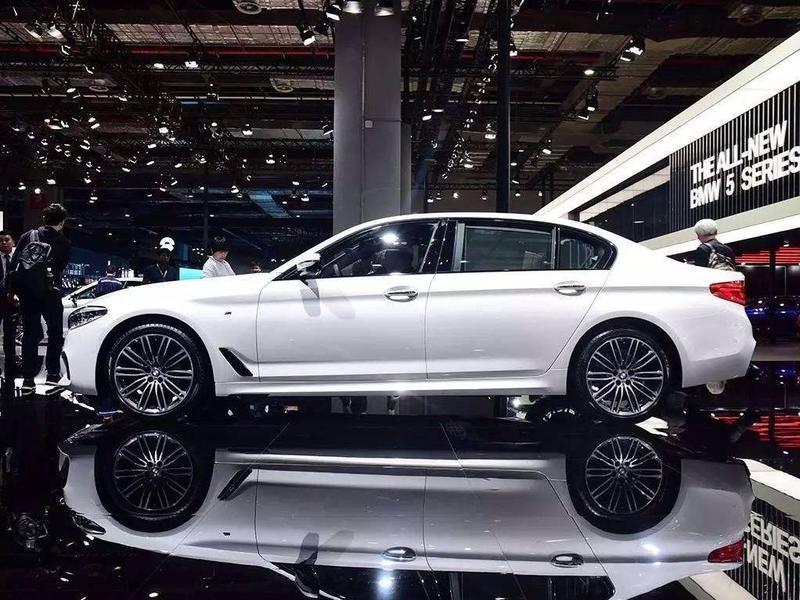
开车并不是什么新鲜事,但是造车对于绝大多数人来说就很陌生了。宝马新5系Li是宝马ACES战略转型之中最具代表性的产品之一,因此,不只是这辆车本身,就连生产出这辆车的华晨宝马新大东工厂也是这么一座结合了ACES理念的工业4.0工厂。
就像把大象关进冰箱里一样,造车也可以通过车间的不同大致分为四步。当然,如果严格仔细的按照步骤来分是要有几百步的。
第一步:冲压车间
进入华晨宝马新大东工厂就能看到冲压车间了(press shop)。冲压车间主要是用于制作汽车的板料,也就是白车身上那些表面光滑的金属半成品。
在冲压车间之中,板料从入库到库存,再到涂料就占了整个车间的一大半,反而中间的冲压机并没有使用很多占地资源。新大东工厂的冲压机采用的是舒勒(schuler)流水线,与以往相反,这套冲压系统的分本控制是非常优秀的,即使就在3、4米远处,也丝毫听不到冲压过程中的噪音。
作为工业4.0的生产工厂,冲压过程是完全自动化的。上料过后的板料,完全不需要经过人手,就可以抵达尾线质检。理论上来说,这应该是国内最快的生产线。
在冲压车间之中,宝马新5系Li的模具重量为38t,然而其精度能达到0.02mm,也就是3分之1头发丝直径的精度。
新大东工厂的冲压车间还有一套能量再生系统,这是为了降低生产成本而准备的。对比其他车间,冲压车间的能量消耗非常大,因此,这套能量循环系统就成为了大东工厂进入工业4.0的门票。
第二步:车身车间
顾名思义,车身车间就是制作白车身的车间。在这个过程中,机械臂随处可见。因为宝马新5系Li车身比上一代减轻了约170瓶水的重量,所以宝马需要更高效的钢材和铝材搭配。以单个后门重量来说,新一代5系的后门重量为8.7公斤,而旧5系为16公斤。
新5系后门所选用的材料为铝合金,而旧5系为合金钢。这也就意味着,新5系的后门在塑造过程中,除了要涂胶、卷边,还需要柳接、无钉柳接、压接螺母。最值得一提的是,宝马新5系并没有采用传统的电焊焊接结束,而用的是激光焊接技术。
激光焊接不会像电焊焊接那样在成品上留下一道“伤疤”,同时激光焊接的善后工作也相对较少。更美观而且节省了时间成本。
车身车间的最后一步仍然是质检,不过这里的质检也非常“工业4.0”。新大东工厂的质检方式是激光质检,通过工作人员手持的扫描仪,电脑中会构建被质检产品的三维模型。这种激光扫描的结果拥有更高的精度,更容易发现问题。
第三步:涂装车间
这回就不是顾名思义了,而是名不副实。涂装车间所做的事情不只是给白车身一点颜色看看,还要让车身具有防腐性、防水性、防石击、高强度、隔噪音、表面光泽,以及防紫外线能力。所以,新5系Li白车身在这里要经过:预处理、电泳、电泳烘干、防撞梁打胶、空腔注蜡、发泡、细密封、底部密封、密封烘干、面漆、面漆烘干、清漆等等。
新5系Li配色集锦
但是,宝马涂装车间是不会产生修补的,其奥妙就在于新大东工厂的在线工艺控制。传统色漆(basecoat)过程中,是不存实时监控的,所以才会在车身离开烘干炉后需要修补。新大东工厂采用实时监控的后台系统,不仅不会产生修补,还能实现膜厚的精度控制,保证了油漆性能。
新大东涂装车间在工业4.0的配合下,能源消耗、水消耗、挥发性有机化合物排放以及废水排放都相对较少。
鉴于卫生需求,涂装车间是不允许游客进入的,即使是我这么爱干净的人也不例外。
第四步:总装车间
总装车间生产的就是成品汽车了,和传统工厂相比,大东工厂的总装车间采用了数字化生产系统。质检、物流、设备管理均联网完成。以无线安灯系统为例,员工和段长通过此系统串联,一方面能保证员工按照生产节拍输出质量稳定,另一方面可以通过数据分析来预测潜在危险,并进行主动防范。
在总装车间之中,宝马也采用了大数据分析。所有关键工序都采用最高精度的电子控制系统,每天会产生14万次的打紧数据,同样也是用来预防质量危险。
在总装车间之中,量产工装卡具是用3D打印技术制作而成的,通过工程橡胶取代了传统的合金材料。在质量上减轻了6KG。
上为新卡具,下为旧卡具
顺便,我也看到了一个非常有趣的装备,这种装备叫做外骨骼“无座座椅”,工人在保持半蹲的姿态下,不需要调节就可以得到外骨骼的支撑,以降低劳动强度。
如何体现ACES?
在参观完了华晨宝马新大东工厂以后,我和宝马集团的董事,齐普策(Oliver Zipse)先生简单的聊了会天。我向他询问,宝马一直在强调ACES战略,那么这个生产过程中,是否也在体现呢?齐普策这样说道,
在我们整个生产过程中当然会体现这一战略。比如大量运用到自动化的物流系统,很多物流物件可以自动地通过轨道车进入到指定工位。在互联互通性方面,我们很多生产流程,以及很多的工位之间有很多数据化的连接。电气化自然不必多说,这是必须的。此外,我们在整个生产车间也有很多的共享服务,是对共享这一理念的实践。可以看出,无论是在产品还是在生产方面,宝马集团的ACES战略都是有所体现的。
众所周知,工业4.0较之前相比,最大的特点是设备联网、数据分析。这其中会产生两种数据,一种是运营数据,像是材料消耗、机器使用频率之类的。宝马将其称作是“慢数据”,通过云端技术,把这些数据结合生产体系。什么时候该维修机器,什么时候该置换机器,通过这些数据一目了然。这样做的目的是降低运营成本。
另外一种数据叫做实时数据,在医疗体系中则叫做临床数据,而在造车的工艺流程之中,宝马可以借此更好的控制细节。比如我们每一次拧紧螺栓,宝马都会把螺栓拧紧的程度进行记录,这些数据被记录下来之后,让宝马对每一次相同的操作进行有效的监测和监督,以便在可能出现问题的时候及时采取干预的措施,防止质量问题的出现。
汽车是一件整合了大量产业链的产物,所以才被称为工业的代表。造车也远比想象中的复杂许多,但是当互联网技术,以及数据分析等等新生元素融入到生产体系时,造车就从手艺活,变成了技术活。